Quick summary for those who need to decide now
If you’re looking for the most suitable material for your professional application, here is a quick comparison of the five filled polyamides we analyzed, based on technical data obtained from injection-molded test specimens:
Material | Key Strength | Ideal for… |
---|---|---|
PA12 CF | Maximum stiffness and toughness | Structures subjected to high static and dynamic loads |
PA12 GF | Good stiffness-to-flexibility balance | General-purpose mechanical components requiring robustness |
PA12 KF | Self-lubricating, extreme elasticity and impact resistance | Sliding parts, hooks, clips, flexible systems |
PA12 CKF | Self-lubricating with a good stiffness-to-flexibility balance | Mixed applications requiring smooth sliding and durability |
SP4CF15 | High thermal resistance and stiffness. Prints in an open chamber. | Complex technical parts 3D printed even on desktop printers |
Try the PA12 fiber-reinforced KIT BUNDLE.
👉 Subscribe to our newsletter to receive technical updates, video tutorials and early access to new materials.
Introduction: Filled Polyamides and Industrial 3D Printing
Polyamides (nylon) are high-performance engineering materials used in numerous industries for their excellent mechanical strength, chemical stability, and good processability. In particular, PA12 stands out for its low moisture absorption and high dimensional stability.
In an additive manufacturing context, fiber-reinforced polyamides (carbon, glass, aramid/kevlar) deliver enhanced performance, making them ideal for producing structural, functional, or hostile-environment components. In this article we examine five materials based on laboratory data obtained from injection-molded test specimens, a method that ensures stable and comparable results.
Five parameters
The parameters chosen for this comparison were selected to provide a reliable technical overview focused on the practical use of the materials in industrial or professional applications. Each one represents a key characteristic of the mechanical and thermal behavior of filled polyamides:
- Impact resistance (Charpy): evaluates how the material behaves under discontinuous mechanical loads, vibrations, accidental impacts, or impulsive movements. It is a critical parameter for components exposed to impacts or installed in dynamic environments.
- Elongation at break: measures the percentage deformation a material can withstand before breaking. It is an indicator of ductility and is very useful for assessing suitability in safety components, end-stops, or flexible supports, where impact absorption without fracture is essential.
- Elastic modulus: indicates the toughness and stiffness of a material, i.e., its ability to resist elastic deformation under load. It is a key parameter in the design of structural components, gears, rigid supports, or mechanical joints.
- HDT (Heat Deflection Temperature): represents the temperature at which the material begins to deform under load. It is essential in environments with high temperatures or constant thermal cycles, such as in the automotive, electronics, or mechanical sectors.
- Density: although the differences among the polyamides considered are modest, specific weight becomes a critical parameter when the design demands lightness, as in robotic, aerospace or motorsport applications.
👉 Thanks to this data, in relation to the intended use of the final part, the user can precisely select the most suitable material, optimizing performance, durability, and machinability.
1. Toughness – Elastic Modulus
The elastic modulus (MPa) measures material stiffness, i.e., its resistance to elastic deformation under stress. It is essential for load-bearing structures and parts that must retain shape and precision under load.
Test method: tensile ISO 527-1.
Ranking – from stiffest to most flexible:
- PA12 CF – 8900 MPa
- SP4CF15 – 8500 MPa
- PA12 CKF – 4500 MPa
- PA12 GF – 2700 MPa
- PA12 KF – 1500 MPa
➡️ PA12 CF is the go-to choice for maximum structural rigidity. SP4CF15, although not PA12, delivers comparable performance and is easier to print.
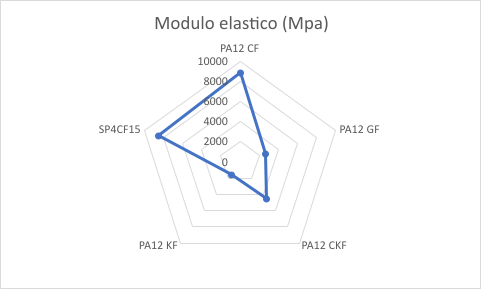
2. Tensile Strength – Elongation at Break
The elongation at break (%) represents the material’s ability to deform before fracturing. It is indicative of ductility and is useful for parts subjected to repeated bending or dynamic loads.
Test method: tensile ISO 527-1.
Ranking – from most versatile to least versatile:
- PA12 KF – 25%
- PA12 GF – 10%
- PA12 CKF – 5.4%
- PA12 CF – 4.9%
- SP4CF15 – 4.2%
➡️ PA12 KF, thanks to the aramid fiber (Kevlar®), is the most elastic material: ideal for flexible parts, sliding components, or items subjected to repeated impact.
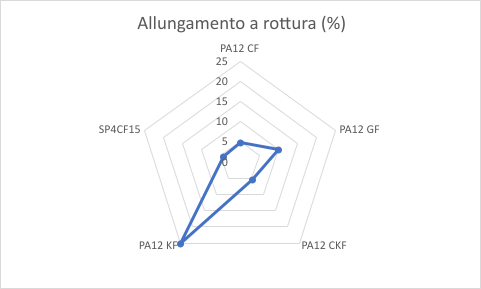
3. Impact Resistance – Charpy Test
The Charpy test measures the amount of energy absorbed by a specimen up to fracture, indicating impact resistance.
Test method: Charpy on un-notched specimen ISO 179-1eU.
Ranking – from strongest to least strong:
- PA12 KF – 65 kJ/m²
- PA12 CF / GF / SP4CF15 – 60 kJ/m²
- PA12 CKF – 35 kJ/m²
➡️ Once again, aramid fiber (Kevlar®) proves to be the winning choice for components exposed to frequent impacts or vibrations.
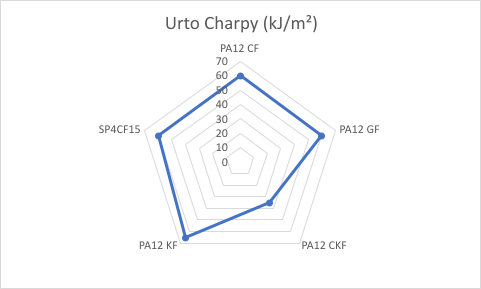
4. Thermal Resistance – HDT at 0.45 MPa
The Heat Deflection Temperature (HDT) is the temperature at which a material begins to deform under a continuous load. It is critical for industrial, automotive, and electrical applications.
Test method: ISO 75, load 0.45 MPa.
Ranking – from most durable to least durable:
- SP4CF15 – 179 °C
- PA12 CF – 163 °C
- PA12 GF – 161 °C
- PA12 CKF – 135 °C
- PA12 KF – 115 °C
➡️ The SP4CF15 is the only material that combines high thermal resistance and desktop printability, making it an outstanding solution for functional prototypes and industrial pre-series.
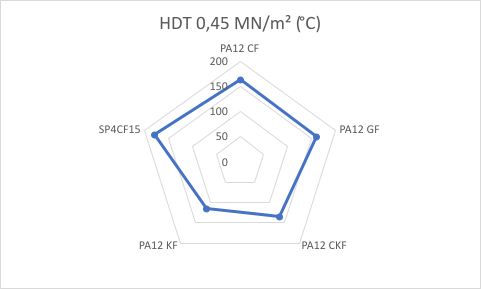
5. Density – Impact on Weight and Design
Density indicates the mass of the material per unit volume (g/cm³) and is critical in applications where weight must be minimized, such as aerospace, racing, or robotics.
Test method: gravimetric measurement on a standardized specimen.
Ranking – from lightest to heaviest:
- PA12 KF – 1.02 g/cm³
- PA12 CKF – 1.07 g/cm³
- PA12 CF / GF – 1.08 g/cm³
- SP4CF15 – 1.19 g/cm³
➡️ PA12 KF is the ideal choice when weight is a critical factor.
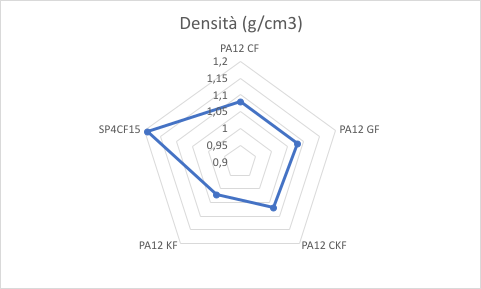
When to Use Which Material
✔️ PA12 CF (Carbon)
- ✅ Maximum rigidity
- ✅ High thermal resistance
- ❌ Low elasticity
Ideal for: rigid frames, structural parts, precision mechanical components.
✔️ PA12 GF (Glass Fiber)
- ✅ Acceptable rigidity
- ✅ Higher elongation than CF
Ideal for: generic components, housings, durable supports.
✔️ PA12 KF (Kevlar®)
- ✅ Extreme elasticity and impact resistance
- ✅ Self-lubricating properties
Ideal for: moving parts, gears, sliding guides.
✔️ PA12 CKF (Carbon + Aramid/Kevlar)
- ✅ Balance between stiffness and dynamic strength
- ❌ Impact-sensitive
Ideal for: mid-level technical applications, levers, joints.
✔️ SP4CF15 (Medium Carbon, PA Blend)
- ✅ Printable with consumer-grade printers
- ✅ Exceptional rigidity and thermal resistance
Ideal for: advanced technical prototypes, functional production runs, critical environments.
Conclusion
Selecting the right material directly affects the functionality, durability, and reliability of the final component. Based on the data analyzed, each filled polyamide finds its ideal application in industrial, mechanical, electronic, or sporting contexts.
A particularly relevant point is represented by the SP4CF15 material: although it is not a PA12, it delivers thermal and mechanical properties virtually identical to PA12 CF, yet with a huge advantage—it is extremely easy to print even on desktop 3D printers, with the same simplicity as a technical PLA.
This feature makes it an outstanding solution for companies, designers, or advanced makers who want to produce functional prototypes or end-use parts independently, without investing in complex professional equipment.
🔧 Unsure which material best suits your application? Contact us or subscribe to our newsletter to receive dedicated technical support.